Thermoplastics
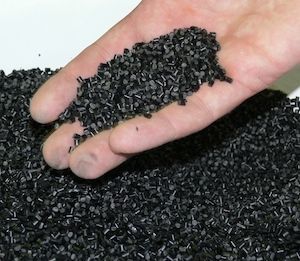
High Performance Fillers for Thermoplastics
The raw materials of HPF Minerals provide valuable services as fillers in many different thermoplastic applications. The reason: the requirements for modern plastics, for example for the automotive industry, are steadily increasing. The polymers alone can no longer meet the required profiles. Therefore they have to be reinforced with high-quality, functional fillers based on the granular cristobalite, the needle-shaped wollastonite and the platelet-shaped mica muscovite and phlogopite. These High Performance Fillers make a decisive contribution to improving the mechanical and thermal properties of the compounds. The use of these functional fillers leads to an increased scratch resistance, to a reduction in mechanical and thermal warping and to an improvement in the tensile strength or the tensile modulus while maintaining the impact resistance in the polymer system and thus in the finished part.
Polypropylene applications
Polypropylene is used in a wide range of applications. It is processed by injection molding into parts for electrical engineering, automotive engineering and household appliances as well as by extrusion into fibers and films. In the last decade, it has been discovered as a material of choice by the automotive industry. Here, large parts such as side, entry or interior panels are made from these compounds.
TREMIN® reinforced polypropylene compounds
Due to the very good reinforcing properties the needle-shaped wollastonite TREMIN® 939 types have proven particularly successful in polypropylene systems. The surface treatment enables an optimized incorporation into the polymer system. Compounds with the following properties can be produced:
-
Excellent impact strength combined with high rigidity
-
Very good scratch resistance
-
High heat deflection temperature
-
Low shrinkage of parts
MICA muscovite and TREFIL® phlogopite for polypropylen/polyethylen-copolymer
By using the platelet-shaped MICA muscovite and TREFIL® phlogopite, the thermal and mechanical properties in polypropylene / polyetyhlene compounds can be significantly improved. This results in a significant reduction in shrinkage in both dimensions as well as an improvement in the heat distortion. An increase in tensile strength and tensile modulus and an increase in stiffness while maintaining toughness are also noted.
Polyamide Applications
Polyamide 6 and Polyamide 66 are the most commonly used engineering plastics in the world. The popularity of these polymers rests on their high thermostability, high hardness and rigidity. Polyamide 6 is additionally characterized by good damping. These mechanical properties are largely determined by the selected fillers.
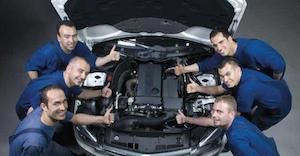
When warping is required, short-needled aminosilan-coated wollastonite powders TREMIN® 283 have been successfully used as functional fillers for polyamides for many years. With the long-needle TREMIN® 939 grades, even higher stiffness can be achieved. The thus reinforced polyamides offer a variety of possibilities for the construction and are used for example in wheel caps, engine covers, air filter housings and electrical equipment parts. They are characterized by excellent stiffness, high heat and temperature resistance and excellent dimensional stability.
Furthermore high impact strength and excellent lacquer adhesion are also achieved.
TREMICA® Muscovite and TREFIL® phlogopite in polyamide 6
The use of surface-modified, platelet-shaped TREMICA® muscovite and TREFIL® phlogopite influences the mechanical and thermal properties of the polyamide compound through a series of positive effects. In addition to increased tensile strength and stiffness as well as reduced shrinkage, an improved shrinkage isotropy and a significant reduction in the heat distortion can be recorded.
SILATHERM® for thermally conductive thermoplastic compounds
Products of the SILATHERM® family increase the thermal conductivity of polyamide and polypropylene compounds significantly and maintain at the same time electrical insulating properties.
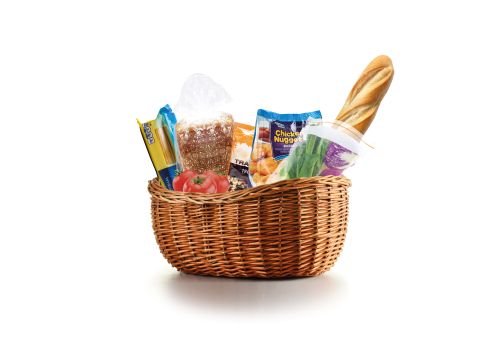
High Performance Fillers for polyethylene films
If films are used to package fruit, vegetables, fish, sausage or cheese, anti-blocking agents are used more or less as a ‘spacer‘ to more easily separate the sides of the film from one another. The effectiveness of the anti-blocking additive is mainly dependent on the properties of the mineral used and the correct grain size. Visual requirements, such as transparency, gloss and opacity, are often added to the mechanical properties. After all, consumers want to see what they buy and therefore gladly reach for transparent plastic packaging.
The following functional high performance additives on a mineral raw material basis are highly suitable for influencing the various desired properties of plastic films:
-
SIKRON® SF 4000 cristobalite fine flour is qualified as anti-blocking additives for transparent films, because of their refractive index nd 1.48 and their grain size distribution
-
TREFIL® 1313 anhydrite flour is a cost-efficient alternative that offers excellent anti-blocking properties but shows slightly elevated haze.
-
MICROSPAR® 1380 feldspar flour exhibits the lowest haze and offers very good anti-blocking values
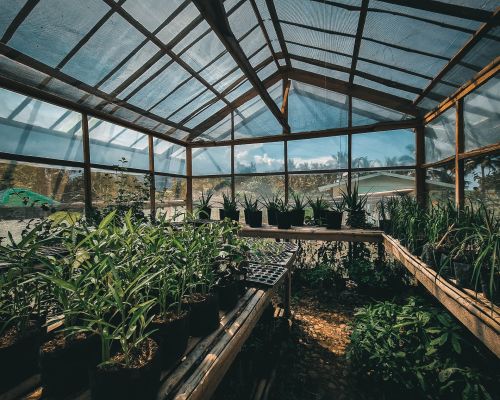
MICROSPAR® 1380 for greenhouse plastic films
Greenhouses made of plastic film offer an economical solution for the intensification of agriculture. This is becoming ever more necessary on account of growing cities and shrinking agricultural areas. Requirements such as UV and IR absorption are the predominant feature in the use of films in agriculture. Sunrays should penetrate the agricultural film slightly to stimulate plant growth. However, the heat should not escape again during the night, but be saved in the greenhouse to compensate for temperature differences and to ensure a uniform temperature for healthy growth of the plants. MICROSPAR® 1380-600 exhibits high transmission values in the range 400 – 700 nm. This range describes the photosynthetically effective radiation.
Please contact us for further information about our High Performance Fillers in thermoplastic applications!